Webbing Factory
Hook Loop Factory Introduction
500,000m2
Plant Area
$90 million
Annual Sales Amount
800+
Workers
1.5 billion meters
Year Production
Hook and Loop Fastener Strap Production Process
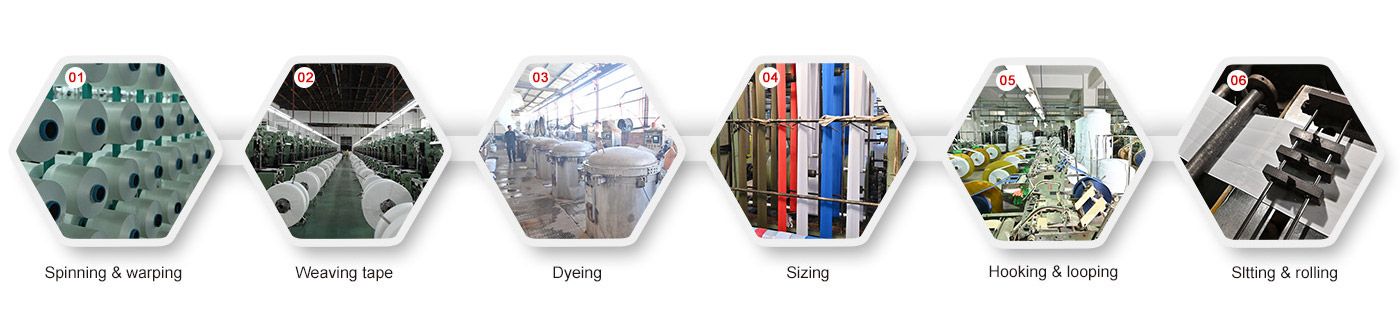
-
SpiningThe process of converting synthetic fibers into fine filaments.
-
WarpingArranging and winding yarns onto a warp beam
-
WeavingInterweaving warp and weft yarns to form tape-like fabric.
-
DyeingImmersing the fabric in dye to achieve the desired color.
-
Sizing
-
HookingApplying a sizing agent (such as polyvinyl alcohol or starch) to the hook fabric to enhance the strength and abrasion resistance of the fibers. Then forming hook structures on the sized fibers through heat treatment or mechanical processing.
-
LoopingUsing a raising machine to brush the loop fabric, making the fibers stand up and form an even loop structure. Then Applying a thin layer of glue, typically water-based or hot melt adhesive, to the raised loop surface.
-
SlittingAccording to order requirements to slit
-
Quality TestingInspecting adhesion strength test, abrasion resistance test, peel strength test, tensile strength test, chemical resistance test, repeated use test, etc.
Elastic Tape Factory Introduction
30,000m2
Plant Area
$20 million
Annual Sales Amount
600 tons
Month Production
Explore the Elastic Webbing Tape Production Process
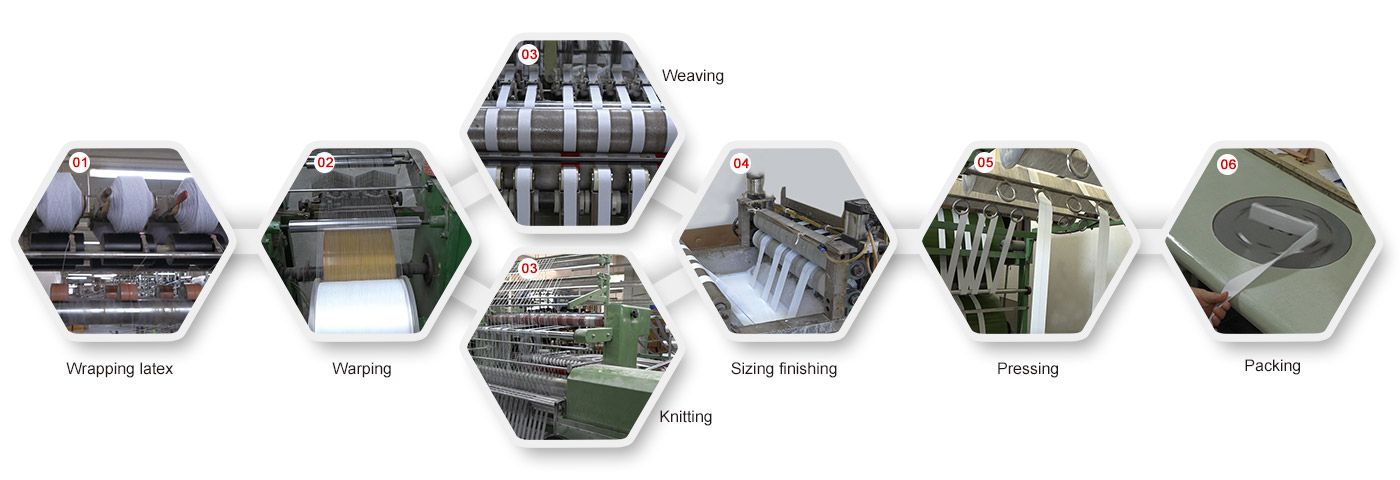
-
Raw materials preparingpolyester, nylon, cotton, polypropylene+latex or rubber
-
Warp warpingArranging and winding the yarns onto a warp beam in a specific order
-
Weft yarns preparingCutting and preparing the weft yarns to the required length and quality
-
Machine setupAdjusting shuttleless loom or jacquard machines for different webbings
-
Drawing-inDrawing the warp yarns through the heddles and reeds of the loom.
-
WeavingInterweaving the warp and weft yarns on the loom to form the elastic band.
-
Quality TestingInspecting the produced elastic bands for quality, including appearance, width, weight, and elasticity ratio.
-
Rolling and packingRolling the inspected elastic bands into rolls, cards, etc.
Bias Binding Tape Factory Introduction
Unveile the Intricate Production Process of Bias Binding Tape
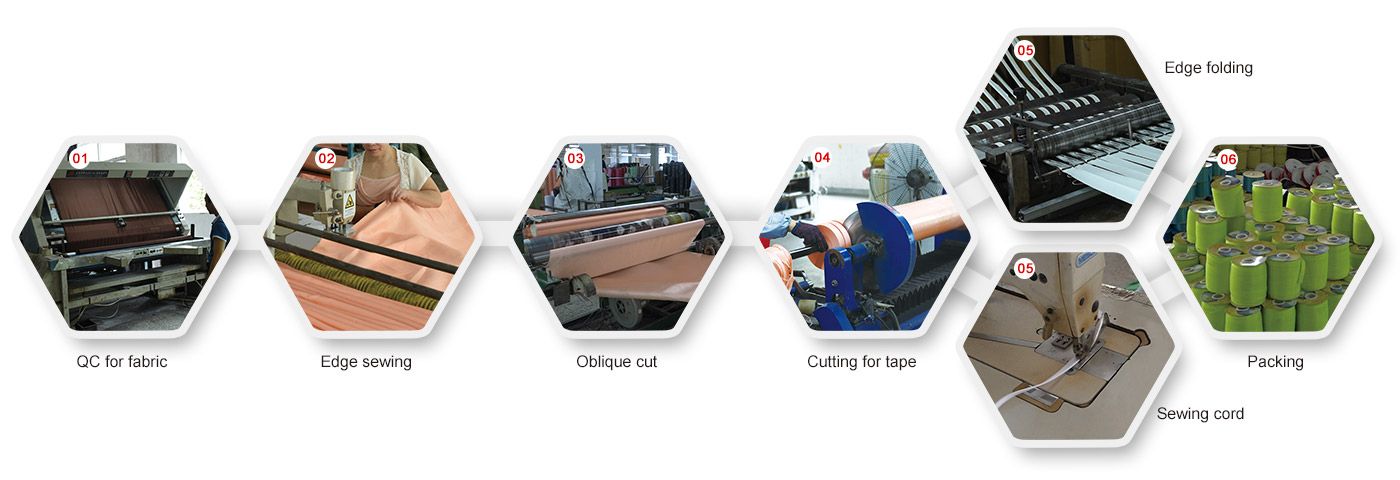
-
QC for fabricsInspect the fabric for quality, including color consistency, thickness, absence of defects, and no stains.
-
Edge sewingSew the edges of the fabric to prevent it from fraying during subsequent processing.
-
Oblique cutCut the fabric into strips at a specified angle (usually 45 degrees) to ensure the bias tape has appropriate elasticity and stretch.
-
Cutting for tapeCut the oblique strips to the appropriate length.
-
Edge foldingFold the edges of the cut strips to form the shape of the bias tape.
-
Sewing CordIf needed, insert a cord into the bias tape to enhance its decorative and functional properties.
-
Quality TestingInspecting the produced elastic bands for quality, including appearance, width, weight, and elasticity.
-
Packaging
Rolling the inspected elastic bands into rolls and packaging them for transport and storage.
Polypropylene Webbing Factory Introduction
30,000m2
Plant Area
$15 million
Annual Sales Amount
12,000 tons
Year Production
1000+
Weaving Equipment
-
WarpingWinding long yarns (warp yarns) onto a warp beam, arranged and tensioned as required.
-
Drawing-inDrawing the warp yarns through the heddles and reeds according to the weaving design pattern
-
WeavingInterweaving warp and weft yarns on a loom to form PP tape.
-
InspectionInspecting the woven PP tape for quality, including appearance, size, and strength.
-
RollingRolling the qualified PP tape into rolls for further processing and transport.
-
Post-treatment SingeingUsing high-temperature treatment to remove loose fibers and excess threads from the surface of the PP tape.
-
PackagingPackaging the processed PP tape into rolls and labeling them with product information for transport and storage.